DEEP FOUNDATIONS
Drilled Shafts
Rooting Out Restrictions
When GROUP needs to get into a tight spot to provide further foundational support to a structure, drilled shafts have proven to be a reliable solution. Remaining relatively unchanged for many years, drilled shaft technology has recently developed to allow for greater versatility in the Gulf Coast industrial space. Drilled shafts are needed in increasingly smaller spaces, which are often sensitive to vibration. Hunter Arrighi, estimator and project manager with GROUP, enjoys the challenge. “Anything is possible with GROUP’s current inventory of equipment,” he said. “It’s just a matter of finding the right fit.”
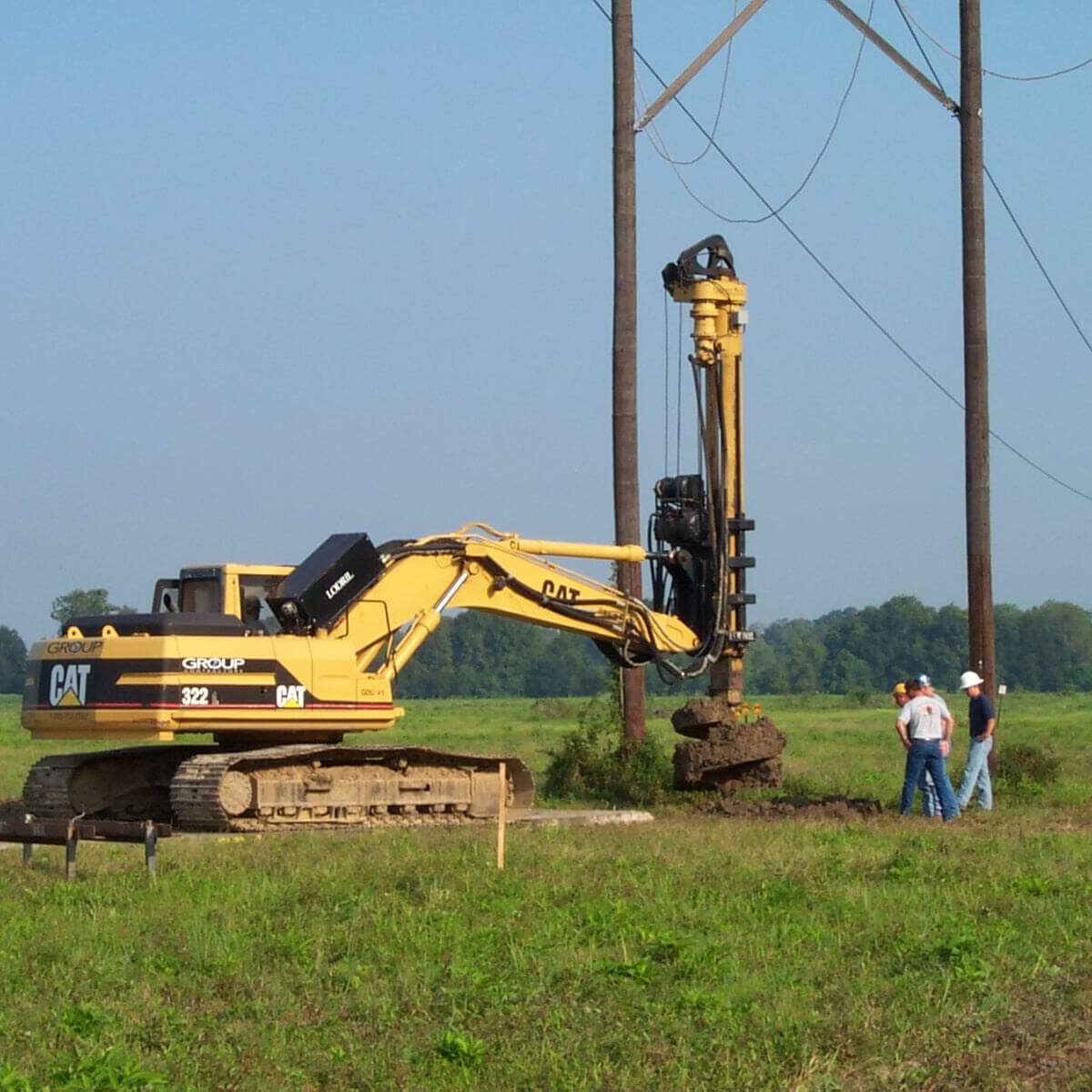
Nothing is lost in terms of strength or stability when considering the smaller size of drilled shaft equipment. “Having that equipment allows us to look at a project differently,” Arrighi said. “If a client has a tough situation and they say it can’t be done, I like to have drilled shafts in my arsenal.”
All of GROUP’s drilled shaft equipment is kept at its Baton Rouge headquarters, including seven drill rigs, an abundance of casing pipe, and various sizes of augers. “It takes a lot of equipment to install drilled shafts, but it’s very cost-efficient, and we can travel with it anywhere.”
“There’s a lot of planning that goes into each project in regards to drilling the shaft, removing the dirt, setting the cage, and so on,” said Arrighi. Arrighi works to accurately price equipment, materials, and subcontractors while simultaneously collaborating with superintendents to determine installation means and methods.
At the surface, constructing drilled shafts appears to be a simple process. The contractor drills a hole to the desired diameter and depth sets the reinforcing steel cage and places the concrete. In reality, it is a more complex process requiring that the contractor understand the various nuances of soil composition and site demands.
Drilled shaft construction can vary depending on the region, soil composition, and client needs. Different soil types require different equipment and drills. For GROUP, the utilization of excavators retrofitted with drill rigs is often versatile enough to perform the work at hand.
To strengthen the foundation of a structure in limited access areas, GROUP often turns to drilled shafts as a dependable and trusted method.
When determining the approach to drilling, three methods can be used and all are depending on soil composition:
Uncased:
- Soil composition allows for drilling without the worry of the integrity of the shaft.
Cased:
- Temporary steel casing is inserted into the shaft, which the contractor drills through to the desired depth.
Slurry:
- The contractor fills the shaft with water and adds a compound to give it a viscosity thick enough to stabilize the shaft walls.
Experience is the crucial factor for success as the contractor often must adapt to unexpected conditions. “Despite what the geography report says, there is always some uncertainty in every job,” said Arrighi. “When you come out of the ground with the auger, for that period of time, the shaft is unsupported, and the ground is trying to push back into that space.
In Texas, for example, we drilled two shafts at depths of 15 feet and 30 feet apart. One was bone dry, and the other had running water in it.” With over 20 years of experience in deep foundations, GROUP has the confidence and ability to respond quickly and effectively to any challenge that may arise.